Albert Einstein famously said, “The definition of insanity is doing the same thing over and over again and expecting different results.”. While this quote is often used to describe various aspects of life, it holds particularly true when it comes to workplace incidents and safety.
Breaking the Cycle of Unsafe Practices
In many workplaces, especially high-risk environments like construction sites or manufacturing plants, safety protocols are put in place to prevent accidents and injuries. Yet, despite these measures, accidents can and do happen. When they do, it’s essential to scrutinize our routines and procedures to understand why.
If we repeatedly follow the same safety practices that lead to incidents, and expect that merely following them again without change will yield different, safer outcomes, we are essentially embodying the definition of insanity. This approach does not address the root causes of the problems and is unlikely to prevent future incidents.
Download this blog as a PDF to review later.
Embracing Continuous Improvement
To truly ensure a safe workplace, we must embrace the concept of continuous improvement. This means regularly reviewing and updating safety protocols, training programs, and equipment. Here’s 5 areas how we can break the cycle of repeating the same actions and expecting different results:
- Regular Training and Education:
- Regularly update training programs to reflect the latest safety standards and learnings from past incidents. Ensure that all employees are not only trained but also understand the importance of these practices.
- Conduct frequent safety drills and workshops to reinforce the importance of safety.
Example: Update the training program to include the latest safety protocols for handling hazardous materials. Conduct workshops to ensure employees are aware of and understand these updates.
Example: Implement regular safety workshops that update employees on new regulations or techniques. For example, if new machinery is introduced, provide specific training on its safe operation.
Example: Regularly update safety training materials to include the latest safety regulations and technologies. Host monthly refresher courses to ensure all employees are aware of and understand these updates. - Management Support: Allocate budget for ongoing safety training and ensure it is integrated into the company’s regular training schedule. Advocate for the importance of safety education in executive meetings.
2. Feedback Loops:
- Encourage employees to provide feedback on existing safety protocols. Those on the frontline often have the best insights into potential hazards and ineffective practices.
- Use this feedback to make real-time adjustments to safety protocols.
Example: An employee reports near-miss incidents involving machinery malfunctions. Use this feedback to adjust maintenance schedules and improve machinery safety features.
Example: Set up an anonymous reporting system where employees can report near-misses or unsafe conditions without fear of reprisal. For instance, if a worker notices a potential hazard in a safety procedure, they can submit feedback that leads to protocol adjustments.
Example: Create a system where employees can anonymously report unsafe conditions or near-misses. For instance, if an employee notices that a machine is malfunctioning, they can report it through a digital form, which is then reviewed and addressed promptly. - Management Support: Promote a culture where feedback is valued and acted upon. Recognize and reward employees who contribute valuable insights.
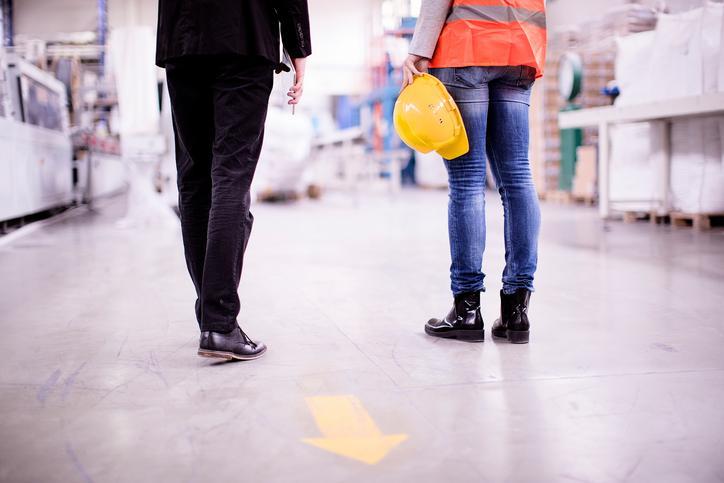
3. Technology and Innovation:
- Stay updated on industry best practices and incorporate them into your safety protocols.
- What works today might not be as effective tomorrow, so it’s important to stay vigilant.
Example: Introduce new wearable technology that alerts workers to potential safety hazards in real-time. This innovation helps prevent accidents and keeps safety measures up-to-date.
Example: Implement new safety technologies, such as wearable sensors that alert workers when they are too close to dangerous machinery. Incorporate these innovations into your safety protocols to enhance protection. - Management Support: Invest in the latest safety technologies and ensure that there is a budget for ongoing technological upgrades. Promote the use of innovative solutions in all safety meetings.
4. Incident Analysis:
- Don’t just investigate what happened; delve into why it happened.
- Use root cause analysis to identify underlying issues and address them comprehensively.
- Understanding what went wrong and why is crucial to preventing future occurrences.
Example: After a worker falls due to slippery floors, investigate the incident thoroughly. Discover that the floor cleaning procedure was inadequate and revise it to include better slip-resistant treatments and regular inspections.
Example: After a machine malfunction causes an injury, instead of merely fixing the machine, conduct a thorough investigation to understand if maintenance schedules or training might need improvement.
Example: After a worker falls from a scaffold, conduct a thorough investigation to find out if the fall was due to faulty equipment, inadequate training, or lack of supervision. Use this analysis to update safety procedures and training. - Management Support: Lead by example by participating in incident reviews and supporting thorough investigations. Ensure that findings lead to actionable changes and follow up on implementation.
5. Adapting and Innovating:
- Implement changes based on feedback and incident analysis. Don’t be afraid to innovate and try new safety measures.
- Sometimes, breaking away from traditional practices can lead to more effective solutions.
Example: Introduce new safety equipment, like enhanced personal protective gear or automated safety systems, based on feedback and recent incident analyses. If feedback indicates a problem with existing safety goggles, test and roll out upgraded versions.
Example: Conduct quarterly reviews of safety procedures and incident reports to assess their effectiveness. Adjust safety measures based on trends and feedback to address any emerging risks. - Management Support: Champion pilot programs for new safety measures and advocate for their adoption company-wide if successful. Encourage a mindset of continuous improvement and innovation.
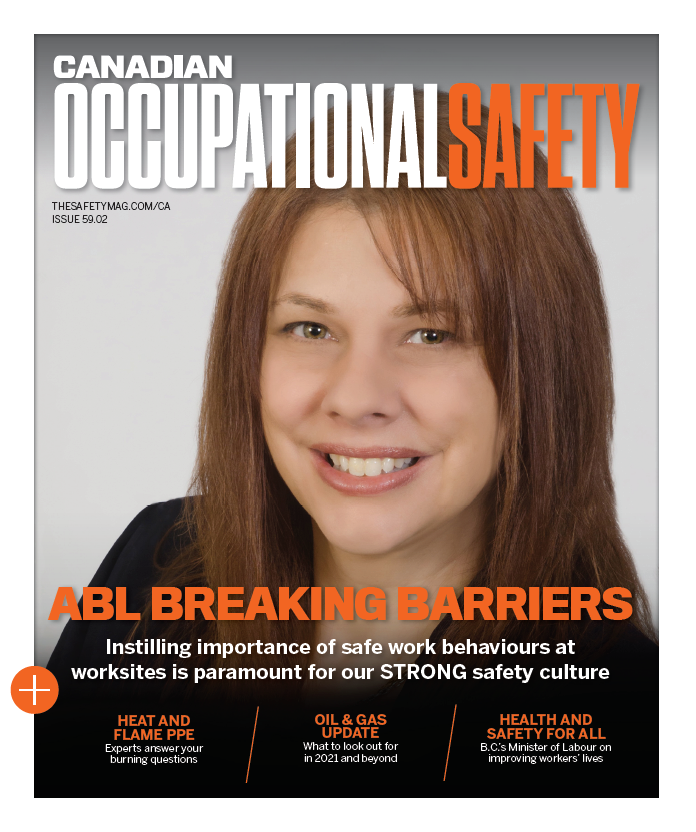
The Role of ABL Employment:
Partnering with a staffing agency led by an Occupational Wellness Manager with over 25 years of experience can enhance workplace safety.
- Qualified Personnel: We ensure that the staffing agency provides workers who have completed industry-specific safety certifications and training before placing them on-site.
- Ongoing Training: offers regular refresher courses on safety practices and updates on new regulations, ensuring all temporary and permanent staff are current on safety requirements.
- Safety Culture: emphasizes a strong safety culture, including safety briefings and protocols that align with your company’s safety standards, helping to instill a shared commitment to safety.
- Compliance Assurance: conducts audits to ensure that both their staff and your workplace are compliant with health and safety regulations, helping to avoid potential violations.
- Flexibility and Adaptability: can quickly adjust staffing levels during peak times or in response to new safety requirements, ensuring that safety standards are maintained without overloading your permanent staff.
Conclusion
Einstein’s definition of insanity serves as a powerful reminder in the realm of workplace safety. If we find ourselves stuck in a cycle of repeated safety incidents, it’s time to change our approach. Einstein’s definition of insanity underscores the need for change when safety issues persist. By embracing continuous improvement and collaborating with a well-equipped staffing agency, we can enhance workplace safety and protect our most valuable asset—our people.
Contact Carla:
carla@ablemployment.com